Presented by: • Andeka Ocio – Manufacturing and Process Validation Technician • Robert Martindale – Product Sales Manager In this webinar you will:
- The main objectives and a step-by-step guide to consider when making any process improvements
- How to manage changes and automations for scaling up processes; efficiently matching higher throughput
- How to circumnavigate common pitfalls, using real industry examples
With increasing diagnostic capacities and the advent and availability of novel therapies, the global biopharmaceuticals industry has been expanding at an extraordinary rate. To meet the rising demands from existing and developing markets, not only is it important to build a robust workflow but also to continually think of process improvements that can be leveraged to enhance productivity, save time, reduce costs, minimize contamination, and meet the needs of an application that requires rapid scaling up. Improving any process in your biopharma workflow requires thorough, step-by-step planning and consideration. In this webinar, we will follow Progenika Biopharma, a Grifols company, on the journey of how they enhanced the filling processes for their kits, accommodating the need for bottling different volumes of solutions and reagent without compromising on accuracy or precision. The final filling mistakes within bioprocessing are far too expensive to be allowed or tolerated. Continuous optimization is a commitment all companies need to embrace to increase the business profitability potential. Evaluating and utilizing new technologies will enable a faster methodology of process, increase the scaling up of bioprocesses, and increase the accuracy of the final filling dosage. In turn, this will optimise the time needed per sample and increase the product output potential, while consistently reducing cost. Masterflex®, a part of Avantor, has developed a range of solutions that illustrate process improvement options and enable customers to make informed decisions when selecting equipment and consumables. Presenters 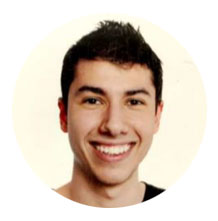 Andeka Ocio — Manufacturing and Process Validation Technician, Progenika Biopharma Andeka graduated with a Biotechnology Bachelor’s Degree from the University of the Basque Country. Shortly after, Andeka found his passion within the pharmaceutical, biotechnological, and bio-healthcare industries. For the past two years, Andeka has been working within the production area of Progenika Biopharma, a Grifols company. Andeka is responsible for the validation and optimization of the manufacturing process. He has implemented several in-process quality controls, scaled up different processes, helped to minimize manufacturing errors, and increased process efficiency while reducing costs.  Robert Martindale — Product Sales Manager, Masterflex® Rob is the EMEA product sales manager for Masterflex, a part of Avantor. Rob’s primary focus is introducing the steady stream of new innovative products into the marketplace. He assists our vast and experienced sales team as they provide our customers with application solutions incorporating our Masterflex pumps, pump tubing and single-use technology. Rob has 20 years of experience working within manufacturing of medical devices. He began his career as a mechanical design engineer. Questions & Answers from the live event The consumables of the pump are just the tubes? Can they be reused or are they single use? Yes, the precision peristaltic tubes are the only consumable component that you need to run the pump. You can reuse the tubes. They are quite resistant to hours of work. When we started using the pump, validating the process, setting all the materials we needed, etc., we also tested the tubes to see if they could be reused. We ran a tube for hours to see if the performance went down, but it resisted well, maintaining good precision and performance. So, we validated a cleaning methodology for the tubes. First, we limited the use of the tube to one and only reagent. After dispensing a buffer, we cleaned the tube, so it was ready for another run, but only used it for the same buffer, reducing the risk of leaving some traces of a different reagent in the tube. Using the same reagent mitigates that. After this, we performed the cleaning validation process and some experiments after cleaning the tube to test the tube. If you run pure water through it, you obtain just water with no contaminations from the buffer. However, cleaning the tubes requires some time, around 20 to 30 minutes in our case. And we found out that for bigger lots or expensive reagents, it is more efficient to throw away the tube and save the time rather than the money you save reusing it. How long can the consumable tube run for? Depending on the duty of the pump, for example a pump running for two hours per day, the tube could last for several months. We generally find that it is the process QC that governs the rate the tube is changed as opposed to the necessity to change the tube through tube wear. Andeka, you went through a decision-making process where you decided that using pipettes was no longer viable and that moving to a peristaltic pump was more efficient and cost effective. What advice could you give to someone who is currently looking at their process to become more efficient and potentially save money? From experience, the decision was forced when LOT sizes became too large for the old process and also to reduce the risk of QC empty bottles. We looked to reduce time by moving to a pump option. I would suggest others look at what they would like to improve in their process and look to the market for relevant options. How much time does it take to set up the pump prior to dispensing? You can quickly add the tubing, calibrate the pump, set the parameters, and start pumping. You could further reduce the programming time during each setup by using the save and recall feature available on the new Masterflex® MasterSense™ pump, where you can save your most used or favorite protocols and recall them very quickly. |